As plans for oil and gas decommissioning projects in the North Sea continue to build momentum, Scottish metal reprocessing, steel trading and environmental services company the John Lawrie Group has been steadily developing its capability to recycle redundant subsea materials including flexible risers, flowlines, and umbilicals.
The Aberdeen-based firm is the leading reprocessor and exporter of scrap metal in the north and north-east of Scotland, and its Aberdeen, Montrose and Evanton recycling facilities are now all capable of receiving the redundant materials for processing. Its expansion into this market comes as oil and gas operators face pressure to increase the amount of redundant material that they recycle.
Environmental director Ray Grant said: “Every business is being encouraged to be more environmentally conscious and recycle more of its waste. Oil and gas operators are also facing these pressures, particularly when they approach decommissioning and look at all the available options for disposal of assets and equipment.
“The development of this service underlines John Lawrie Group’s commitment to maximising the recovery of waste products in an environmentally acceptable and sustainable manner. Many companies are striving to improve their environmental credentials and recycling redundant assets and equipment is a sustainable process which can achieve this objective.”
The recycling process involves mechanically separating the riser’s various plastic and metallic components, which typically consists of between six and eight layers. Once separated, the recovered metallic and non-metallic material is sorted into its various component parts to maximise recycling.
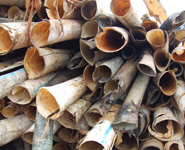
The separated metal content is processed on-site to European steel mill feedstock standard. This material is then shipped and exported as a ‘green waste’ directly to approved steel mills in Europe for recycling into new steel products. All the recovered plastic material is transferred to authorised recycling contractors for further processing before being made into new products.
Mr Grant added: “Every effort is made to recycle as much material from the risers as possible. The success varies depending on the materials used to construct the riser, but the process has seen up to 100% of all material being recycled.”